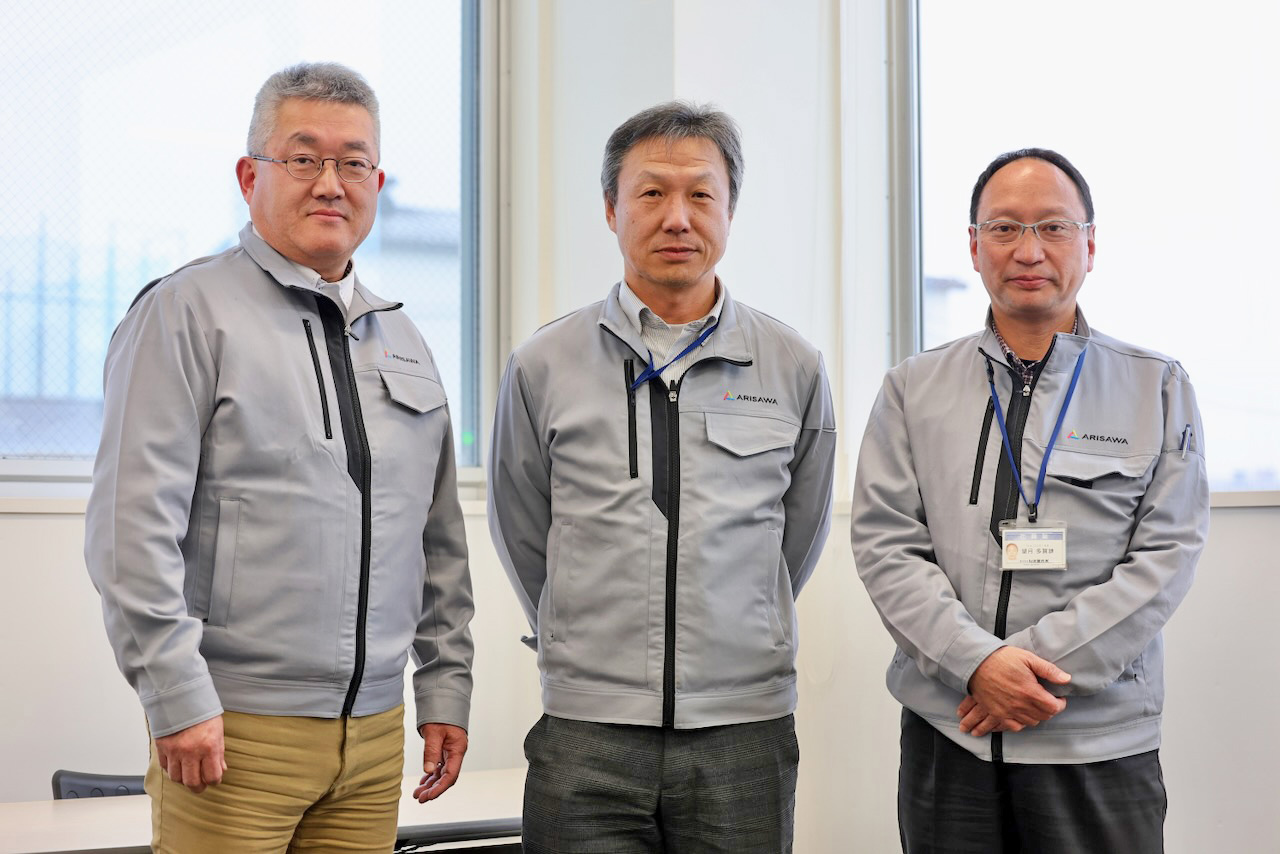
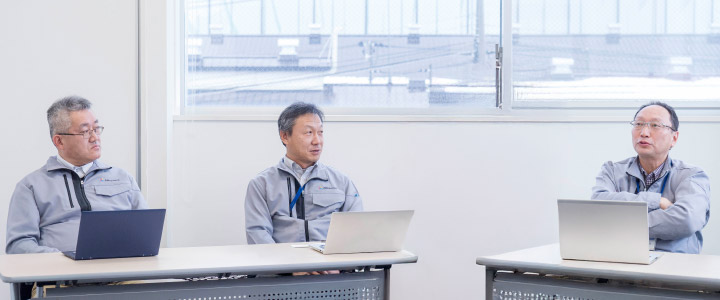
「未来のピースができるまで」では、当社がこれまでに生み出した“未来のピース”を取り上げていきます。ふだん知られることは少ないですが、当社は、世界に誇る日本発の未来の技術を開発しています。シリーズ第4回は、他にない有沢の技術と品質を実現する上で欠かせない、製造部門の品質向上の取り組みについて語ります。
高品質で作り続けることや安定して供給し続けること、そのことでお客さんに信頼をしてもらえることについて、どんな考えをもって、どのように取り組んできたのかをお聞かせください。
野島:私は製造部門が長いですが、やはり当社でしか作れないものを作ってきているのは間違いないと思っています。また何でも1番が好きな人間なので、世の中に向けて1番でありたいと思ってきました。以前は「これは有沢製作所が1番」というものがたくさんあったような気がします。当社は、ニッチで他社が作らないもの、言い換えれば「世界で1番」と言えるものを作ってきました。最近はいろんなところが参入してきて、以前に比べて競争が厳しくなってきていると思っています。その中でも勝ち残っていきたい、当社のものが1番だっていう気持ちを、従業員がしっかり持っていると思うので、かろうじてまだ1番でいるかなと思っています。
相澤:私は入社して最初は開発部門に配属され、その後、製造をサポートする製造技術部に異動しました。そこではもう「昼市(ひるいち)」という仕組みがありました。製造技術部でプラズマディスプレイの前面板の生産販売をしていたときですが、昼市に参加すると、製造部から「不良が出ているけど、どう改善していこうか?」と、入れ代わり立ち代わり、いろんな人が次々とやってくる。当時は課長職が仕切って昼市を行っていましたが、不良品が出たり、生産性が悪かったりすると、みんな顔色変えてね。毎日のように質問攻めに会いました(笑)。改善を求められて、その都度提案を持って行きましたね。それが2000年頃です。
そうこうしているうちに製造部へ異動になり、その時には昼市を使って、製造部内にもいろいろな改善を要求したり、製造部内でできないことがあれば外部に発信したり、そういうことで昼市を活用してきました。2003年から21年まで製造部にいたのですが、この昼市という手段を使って、いろいろな改善に取り組んできましたね。
製造部と製造技術部の仕事の違いは?
相澤:マニュアルに沿って、同じ仕事を誰でもできるようにしていくのが製造技術部の仕事です。標準書と呼ばれるマニュアルを作ります。製造の担当者がものづくりをできるように、コンテンツを作るわけです。最初から完全なものにはならないので、製造部のいろいろな意見を吸いあげて、日々改善していきます。やり方を変えることによって、より良いものができていくわけですね。常にPDCA(1)を回しながら、マニュアルを洗練されたものにしていくのが仕事です。
(1) PDCA:Plan(計画)、Do(実行)、Check(評価)、Action(改善)の頭文字を取った言葉で、業務改善や品質改善、目標達成に用いられる手法
トヨタの「カイゼン」みたいな?
相澤:そう、トヨタのTPS(Toyota Production System)を当社で導入しました。1997年頃に勉強会が発足して、そこからスタートしています。
望月:私は入社してから長く生産技術部というところで、側面から製造部をサポートする立場にいました。設備の導入や、独自性のある機械を作ることが仕事です。他社と差をつけるような設備の導入をサポートしてきました。その後製造部に異動になり今に至りますが、当社は製造会社として、単に1つの機械を入れるのではなく、いろいろな過去の知見を活かして新しい機械を入れているという経緯がありますね。そこが当社の強さなのかなと思います。あとはやはり地域性というのがあるかと思います。雪国で育った人の性格なのだと思いますが、非常に忍耐力があるところと、すごく真面目な人も多くいます。そういうところが繰り返しものを作るということに関して安定して取り組めている一因なのではと考えています。製造業を始めて100年以上になりますが、本当に先輩方が作ってくれた製造の安定感というものがあり、今現在は一昔前と比べると格段にものづくりが安定していると感じています。10年、20年前は、昼市活動でも議題が多かったのですが、直近では全くトラブルがないという日も多く、通常の会話で済む場合もあります。やはり先輩方がものづくりの改善を繰り返してくれたおかげで、今日があるのかなと感じています。
他がやらないニッチな領域で、有沢製作所が1番のものが多くあったと伺いましたが、例えばどんなものですか?
野島:1番といえば、当社の売上の多くを占めるフレキシブルプリント基板の材料ですね。この分野での当社製品は高い世界シェアを占めていました。スマートフォンが出てくる前はフリップタイプといいますが、開くとか、スライドするような携帯電話でした。そこに入る当社の材料が、切れない・断線しないということでシェアを拡大しました。他社のものより断然長持ちしました。通常、ヒンジのところは何回も開閉すると切れてしまうのですが、当社のものは20万回ぐらい耐久性がある。しかし他社のものは数万回で切れてしまうと。圧倒的な性能差が出せていました。ところがスマートフォンに変わったことでそれが必要なくなってしまいました。独占ではなくなって、仕様も変わってきて。それまではポリミドフィルムという、耐熱性の高い材料に、接着剤を塗って、銅箔を張った3層構造の材料だったのです。それがポリミドの材料に直接銅箔を貼るという2層構造に変わって、どこでも同じようなものを作れるようになってしまいました。そんな中でも当社の品質を評価していただいて、品質が良いということで未だに高いシェアを維持しています。
銅箔はすごく薄いもので、私たちはロールを介して作っていますが、ロールの上に1つ小さな異物があるだけで、それがずっと同じところに押し跡をつけてしまいます。当社のものはそれが極めて少ないと言われています。その違いが品質の差ということになります。当社よりも歴史の浅いところは、その部分に対する対策がまだまだなされてない。当社では、他社が同じことを簡単にできないようなところまでやっている。実際には機械が製品を作るのですが、人が介入して、どうやって欠点を出さないようにするかを日々追求しています。それこそが当社の技術力だと思います。
最後は人の力が品質の差になっているのですね。
相澤:あとは、設備を作る力が勝っているのだろうなと。機械を買ってくれば製品ができるわけではありません。買っては来るのですが、自分たちで機械を改良するわけです。人間が介在する作業っていうのは必ずあって、先ほどの押し跡などが出ないようにハンドリングすることも強みの1つです。装置を補完しながら総合的に作っていく。製造設備と人と材料をうまく組み合わせて、より高品質なものを作り上げるのです。
同じ機械でも、動かす人の取り組み次第で品質差が出るのですね。
野島:大胆な話をすると、自動化されて、きれいに掃除機が回っている工場にはゴミが入らないのかなって思いますよね?ところがそうではない。だから当社では、雑巾がけをしています。クリーンルームにある機械の周りの床を、絞った雑巾で人間が雑巾がけしています。でもそれが根幹ですよね。まさかっていう人も多いでしょうけどね。みんなが半導体を作る工場のようにクリーンウェアを着て、仕事をしている。その中で、専用の雑巾をぬらして絞って、一生懸命に拭いています。
先ほど質問攻めにあったとおっしゃっていましたが、今まで、ここが大変だったという事例はありますか?
相澤:材料を100仕入れたら、100すべてが製品になることを求めるのが製造部の仕事です。ところが開発部というのは、80ぐらいまでできる目途が立てば、製造部に引き渡して量産に入ってもらいます。製造では80%の完成度のものを100%まで持っていく。その過程のなかで、いろいろな失敗談はあります。お客さまから全部駄目と言われるときもありました。100作ってゼロ、全部やり直し。こんなもの買わないよと言われたケースもあります。後出しで要求が厳しくなることもありました。抵抗しても無駄なので、根本から作り方を見直さなければいけないわけです。そういうのは製造の失敗というよりも、最初の製品仕様の詰めの甘さが失敗の原因ですね。当初のオーダでは大丈夫なものが、途中で仕様が厳しくなってしまうというケースもあります。そうすると100製造した内の、50も仕様をクリアできないとか、不良の山になってしまうのでそれが一番困る。
野島:たとえ話ですが、技術部が開発する段階で、100個作る中に30個は駄目なものがあってもいいようにお金の原価を決めているのです。だから7割が製品として販売できれば十分利益が出るし、技術部はそれで良いと考えている。だけど製造部で実際に製造して、100個作って30個も無駄になっていたら許されません。私たち製造部はもう必死になって、100個作ったら99個生き残るように工程を作るし、物の作り方を追い込みます。それで利益が生まれるわけです。
相澤:例えば、製造時のゴミを限りなくゼロにするために、半導体工場レベルのようなクリーンルームが必要かというと、そこまでではありませんし、そもそも過剰な設備投資は製品原価が高くなる要因になってしまいます。
望月:理想となる目標のクリーン度を決めますが、実際の設備と製造工程による部分がすごく大きい。人が動かなければ、ゴミは限りなくゼロに近づく。でも実際は機械が動いているし、人が動いているし、原材料が入ってきたりする。与えられた環境下で、ゴミをいかに減らすかというのが製造の1つの力だと思いますね。
(後編に続く)