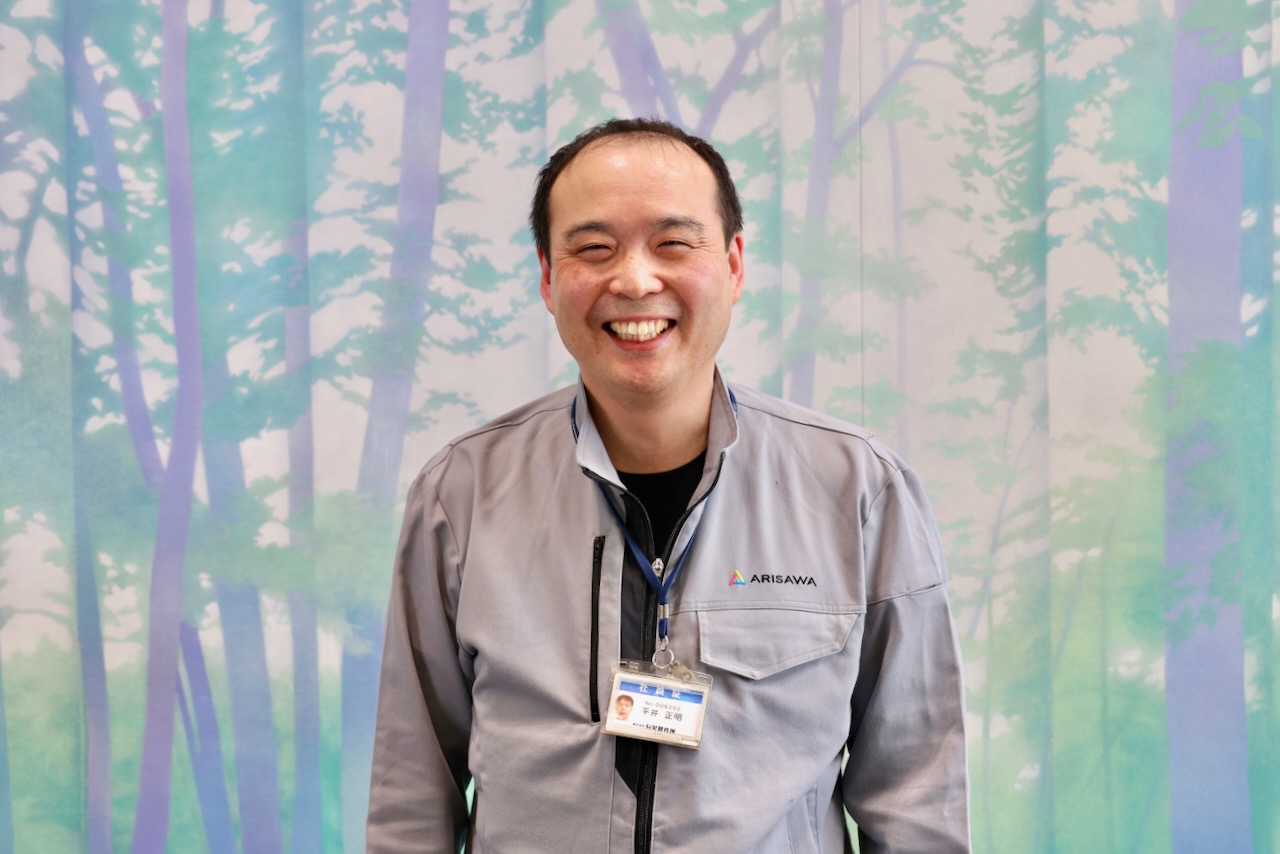
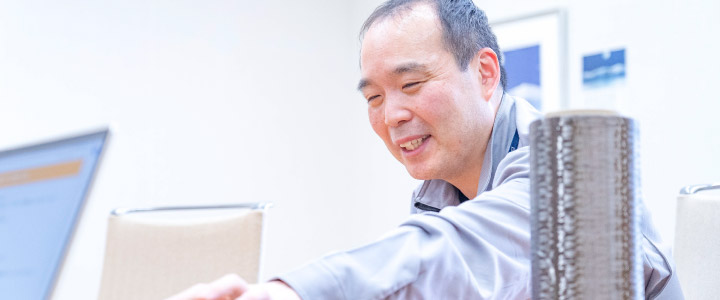
平井正明(イノベーション推進本部 成形材料開発部 主査)
「未来のピースができるまで」では、当社がこれまでに生み出した“未来のピース”を取り上げていきます。ふだん知られることは少ないですが、当社は、世界に誇る日本発の未来の技術を開発しています。シリーズ第3回は、有沢製作所の織る・塗る・形づくる技術の集大成でもある、FRP(繊維強化プラスチック)開発の歴史と未来について語ります。
軽く、強く、燃えにくいハニカムコア
一般の人にはなじみのない、ハニカムパネルについて教えてください。
当社複合材料事業の主力製品に、ハニカムパネルというものがあります。蜂の巣のような形状をした、軽くて燃えにくいハニカムコアを用い、その表裏に強化材を用いた構造のパネルです。非常に軽さを求められる材料で、航空機向けの市場がメインです。空を飛ぶ鉄の塊をいかに軽くしようかという発想で、人類は何世紀も前に、蜂の巣の形状からヒントを得たハニカムコアを生み出したそうです。紙のような素材でスタートしたと思いますが、もっと燃えにくさとか強度を出すために、現在はアラミド繊維を用いたアラミドペーパーでハニカムコアはできています。航空機をより効率よく飛ばすために、こうした中空のコア材料を使うことで、軽くて丈夫な部品を作ろうと。内装材や翼などに、このハニカムパネルが使われているわけです。
確かに軽い。蜂の巣のように、中が空洞だからですね。
航空機の世界で軽くて強いものが必要という需要から、ハニカムコアは開発されています。でもこの紙素材のコアだけだったら強度が足りず使えないので、表裏に強化材となるスキン層を設けることで強度を確保します。このスキン層のところに、私たちの「織る」「塗る」「形づくる」技術を活用しているのです。スキン層の材料として、グループ会社のアリサワファイバーグラスで織ったガラスクロスを採用しています。そこに樹脂を塗ってプリプレグ(1)にする。さらに、それをプレス成形して形づくるという、当社のコア技術を全て使った典型的な材料です。1984年頃に量産を始めて、40年以上も引き継いできたのがハニカムパネルという事業です。それ以外に、このガラスクロス等の基材に樹脂をつけて熱で固めたFRP(繊維強化プラスチック)も複合材料事業の主力製品です。
(1)プリプレグ(通称 “pre-preg”、正確には pre-impregnated):樹脂が含浸されたガラスやカーボンの繊維シートのこと
これはプラスチックのようなものですか?
そう、プラスチックの世界ですね。船舶用などいろいろなところに使われています。自動車だったり、航空機だったり。プラスチックとはいえ、純粋なFRP材料だけだと結構重たくなってしまう。だからハニカムパネルは、中心に入れたハニカム構造のコア材を、なるべく薄く軽くしたFRPのスキン層でサンドすることで、中空層を活かしつつ剛性を出そうという考えで作っています。ハニカムパネルはまさに航空機には持ってこいの、すごくよく考えられた材料です。私がこのパネルに関わって約30年が経ちますが、これを上回る材料はいまだ出てきていないと思っています。私たちの「織る」「塗る」「形づくる」技術を活かすことで、このハニカムパネルはできています。
「織る」「塗る」「形づくる」技術の集大成
この技術は他にも競合メーカーがいると思いますが、他社と比較して有沢製作所の評価はどうなのですか?
競合社には海外メーカーが多いです。その中で当社は、最大手の米国航空機メーカーに納入していることもあり、世界シェアで3割ぐらいは行っていると思います。独自の強みは、技術的な小回りが利くところです。FRPを作るときに「織る」「塗る」「形づくる」の全てを自前でできるメーカーは、たぶん日本では当社だけだと思います。普通は、織りは織物屋さん、塗りは塗り屋さん、成形は成形屋さんなど、分業で成り立っているものです。それを一貫してできることが当社の最大の強みです。
FRPは1984年からずっと生産しているわけですけど、中身は進化しているのですか?
もちろんです。以前の機体内装材に使われたのは、ガラスクロスをメインにしたものでした。ガラスクロスは安価なのですが、今では重い部材でもあります。一方、最新機では、カーボンクロスを用いています。ガラスからカーボンに変えることで、軽くできる。さらに強度は設計次第で同等以上にできます。このハニカムパネルの場合、スキン層の強化材をただガラスからカーボンに変えただけではだめなのです。当社のカーボンパネルは、わずか0.2ミリのスキン層の薄さに、特殊な4層構造を持たせています。そうすることで、従来のガラスクロスを用いたハニカムパネルに比べて2割ほど軽くなっているのに、強度・剛性などは同等以上にできています。そういう工夫をできるのが、私たちの技術ですね。材料だけじゃなくて、材料をいかに成形して工夫して使いこなすかという設計が大切なのです。
これからもさらに進化していくのでしょうか?
はい、これからは軽さだけじゃなくて、環境のことを考えなければならない。時代がバイオマスとかサステナブルとかにどんどん変化する中で、私たちの複合材料も環境に優しいものを目指していかないといけないと思っています。例えば、今はフェノール樹脂を使っていますけど、環境にやさしいバイオマスなどの材料開発にも取り組まないといけません。
当社のFRP製品は、ガラスやカーボンの繊維をメーカーから買ってきて、織ってクロスにしたものを加工したり、フィラメントワインディング(FW)パイプや引き抜き成形にしたりして作ります。ただ、これだけだとやっぱり面白くない。いかにお客さまの要求通りにカスタマイズできるかというところが、私たち技術部門の仕事。例えば、軽くしつつ剛性を高めるということに加え、時代に合わせた環境に優しいサステナブルな製品づくりも並行して考えます。物理や機械工学的な部分と、化学的な部分を上手に組み合わせないと、これからの時代にFRP材料は生き残っていけないですね。私は機械工学出身なのですが、化学屋さんとアイデアを持ち寄って、一緒になって開発していきます。
組織を超えて、何度も会議を重ねて、アイデアを持ち寄ったりするのですね。
新しいイノベーションセンターに向けた準備として、座席のフリーアドレス化が始まっています。もう組織にとらわれず、いろんな分野の人とどんどんコミュニケーションをとって、イノベーションを起こしましょうという活動をしている最中なのです。異なる視点から情報が入ったり、自分の意見を入れたりというのがうまくはまってくれば、もっと面白いものづくりができるはずです。
(後編に続く)