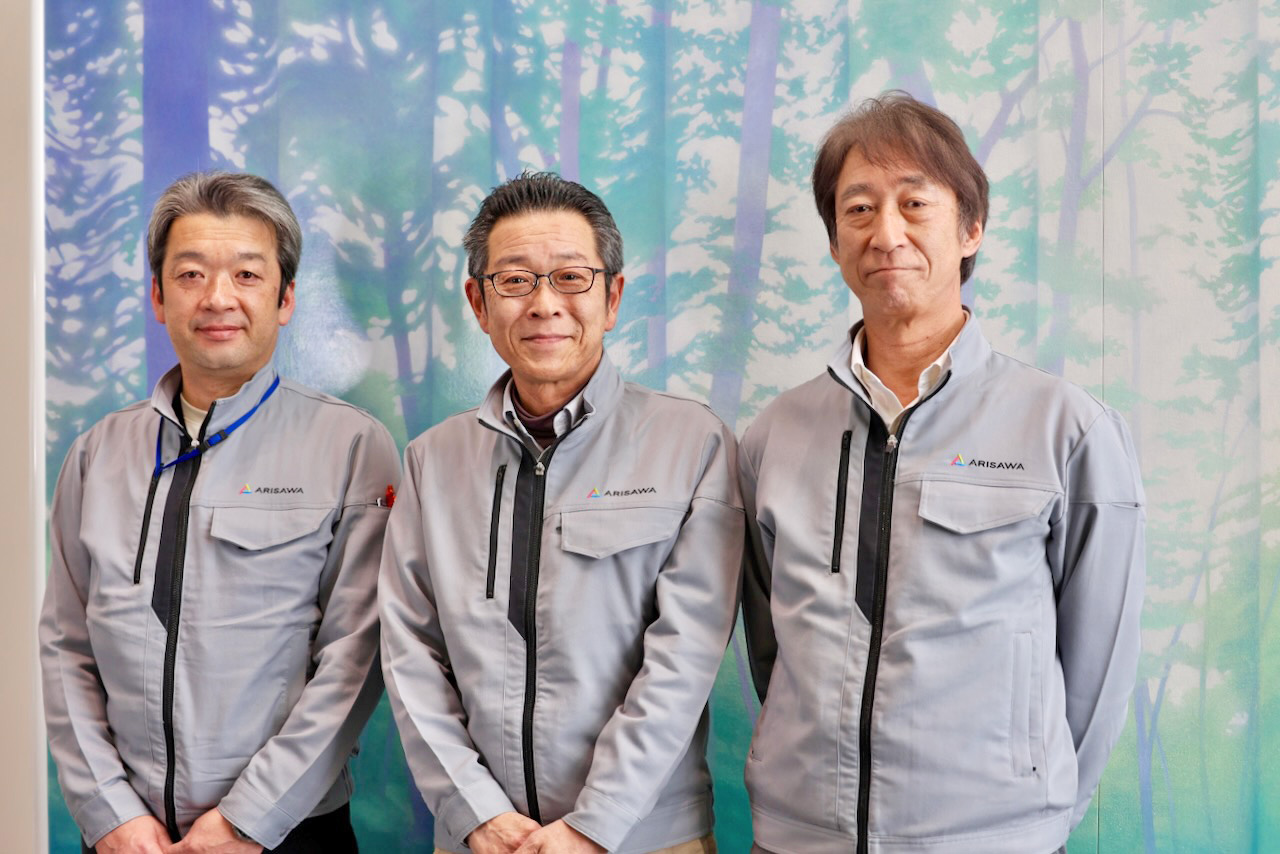
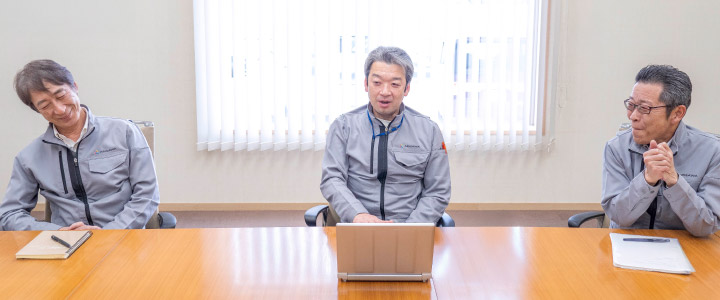
荻野 満(元電子材料製造技術部 執行役員)
「未来のピースができるまで」では、当社がこれまでに生み出した“未来のピース”を取り上げていきます。ふだん知られることは少ないですが、当社は、世界に誇る日本発の未来の技術を開発しています。シリーズ第2回は、有沢製作所の中核事業であり、スマートフォン用で圧倒的な世界シェアを誇る、FPC(フレキシブル基板)材料開発の歴史と、“つながる未来” について語ります。
「塗る」技術のイノベーション。当社の基幹事業がいかにして生まれたか
FPC材料事業は有沢製作所の稼ぎ頭ですが、この分野の始まりから今に至るまでの歴史を教えてください。荻野:私が入社する前の話ですが、最初は国内の某インク会社(A社)との共同開発から始まりました。ガラスクロスに樹脂を塗って、やわらかい板をつくりたいと。当社がガラスクロスの売り込みに行ったとき、その会社ではこういうものをやっているという話題になり、一緒にやらないかと言われたのが最初だったと思います。ガラスクロスはもともと硬い素材ですが、それをフレキ(1)と言われる柔らかい樹脂との中間みたいな形で、良いとこ取りをしようと思って開発していきました。その後A社が、事業転換などいろいろあって撤退することになり、最終的にこの樹脂配合の技術を当社が引き継いで、それを販売していくことになりました。
(1)フレキ: ここではフレキシブルプリント配線板の略語。硬い板状のリジッド基板に対し、折り曲げたりできる柔らかいフィルム状の回路基板をフレキシブルプリント配線板という。
それはいつ頃のことですか。
荻野:確か1970年代です。引き継いだときに、プリント配線板メーカーがちょうどカバーレイフィルム(2)を欲しがっていて、私たちが独自の配合で作り上げたものが採用されました。その頃は、まだ担当した技術者はわずか3人でした。そんな中で、もっと別の種類の接着剤を開発することになり、それを担当したわけです。
(2)カバーレイフィルム:ポリイミドフィルム上に絶縁性接着剤をコーティングした材料。スマートフォン、ノートPC、LCD、HDD、DVD-drive等のさまざまな製品に使用可能な品種をそろえています。高速伝送やファインパターンなどのさまざまな用途に特化したタイプがあります。
わずか3人から始まって、その後スマートフォンで圧倒的な世界シェアを確立するところまでいくことになりますね。どういう発展を遂げていったのですか。
荻野:最初のきっかけは専用機の導入ですね。FPC材料を専門に作る工場を建てたわけです。それまでは塗工グループという、ガラスクロスや紙などにいろいろ塗工している製造グループの中で、機械を貸してもらって塗っている感じでほそぼそとやっていました。
北:専用機ができたとは言っても、取りあえず機械があるだけで、それ以外は何もないわけです。ユーティリティとか、机も椅子さえも。3人で床にダンボールを敷いて、布団代わりにエアキャップで仮眠したりしながらね。でもそれはそれで本当に楽しかった。
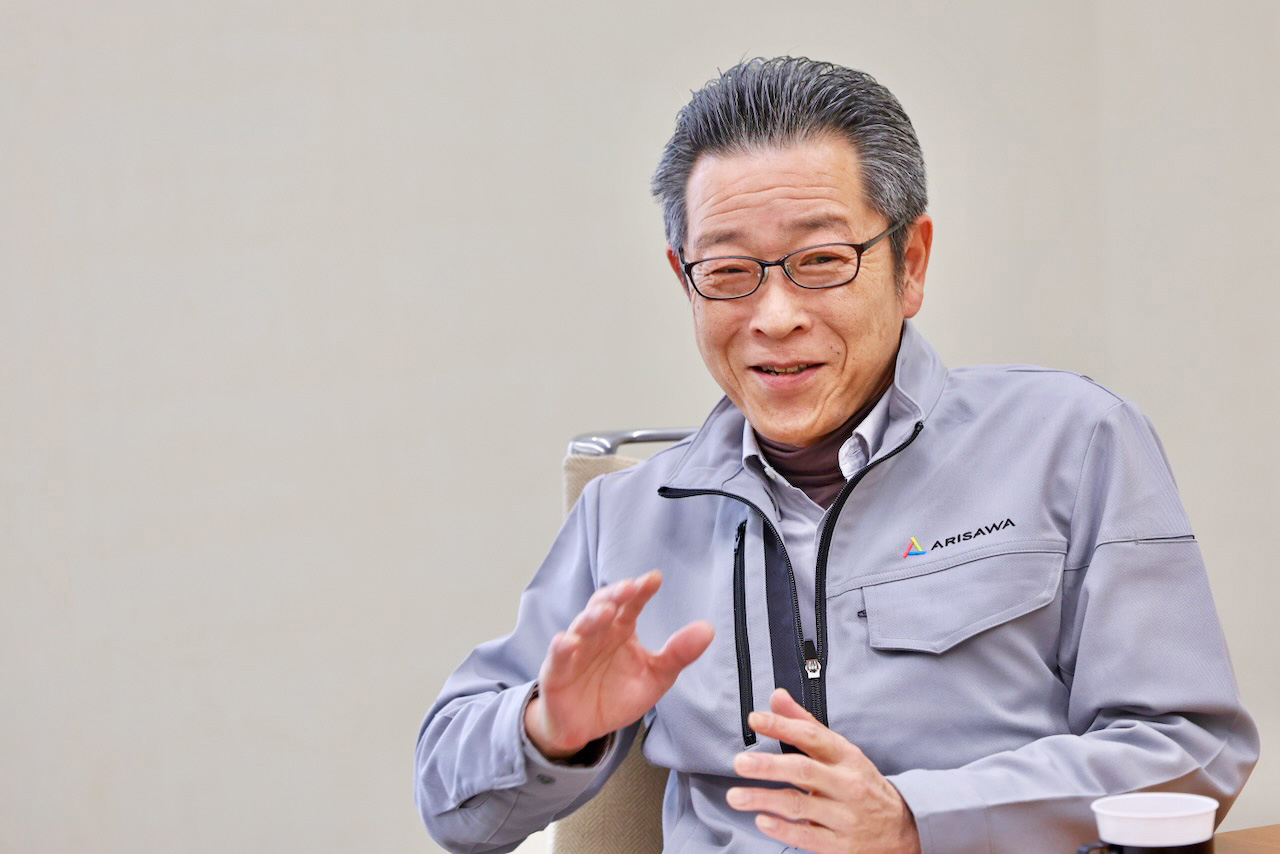
顧客の難題を次々と解決しながら、FPC材料の市場領域を拡大
その塗工機のラインが埋まるほどのお客さんはいたのですか?
荻野:全然ですよ。こまごまと注文はありましたけど…。完全に見切り発車でしたね(笑)。これから拡販しようとしたときに、目的の基板が最初の塗工機じゃできないということが分かって、さらにもう1つ専用機を入れて、そこからPETを使ってインパネ用の基板を作りました。買ってくれたのは車のメーター屋さんでした。PETはペットボトルの「ペット」で、いわゆるPET樹脂のフィルム。昔はそれを基板に使っていました。今の車のインパネには硬いリジッド基板が使われていて、PET基板のものはなくなってしまいましたけど、そんな時代もありました。とりあえず自動車業界に参入したことで、事業は少しずつ軌道に乗り始めたということですね。ここでは品質保証の大変さも勉強させてもらいました。
藤田:他にもいろいろなメーカーさんに採用してもらって売上も伸ばしていきました。お客さんが広がってくると「もうちょっとこういう特性のものができないか」というお話も頂くようになり、その都度、開発を進めていきました。一方、PET基板だけでは将来性に不安がありましたから、ポリイミドを使ったFPC材料の開発を始めました。とりあえずデジタルカメラなどで使えるような基板を作ろうと。
そこで電子部品市場に入っていったわけですね。
荻野:最初はある家電メーカーの小型デジタルカメラ用ですね。折り曲げて配線できる基板を作りました。液晶画面がクルっと回るとか、そういう用途にやっと入っていけるようになりました。
藤田:それから次はハードディスクですね。当時そこに使われているFPC材料で、いろいろな問題が発生していました。古いFPC材料だと、ハードディスクの特性要求を満たすことができませんでした。そこで、私たちがその問題に対応できるものを開発しました。そうすると、有沢製作所は「優れた技術を持っている」と世間から認知され、お客さんも広がっていきました。それが1回目の成長期ですね。
電子部品は非常にシビアな品質を求められるイメージがありますが、ご苦労もありましたか?
藤田:車のときは比較的大きなサイズで、軽くて薄く、電気さえちゃんと通ってくれればいいというくらいのレベルでした。しかし、デジタルカメラやハードディスクとなると小型で、軽薄・短小っていうところにマッチしなくてはいけない。求められる特性や品質は、はるかに厳しくなりました。特にハードディスクの場合は、屈曲性が要求されます。お客さんに求められる基準をある程度予測して、当社で独自に開発しました。それが評判になって、さらに広がっていきました。技術開発スタッフも最初は3人でスタートしたものが倍増し、生産量もすごく増えていきました。
その次に来たのはどのような需要ですか。
藤田:ハロゲンフリーです。世の中が環境重視の時代になりました。FPC材料というのは燃えてはいけない(難燃性)という1つの規格があるのですが、そのために臭素などのハロゲン系化合物を使っていました。しかし焼却する時に人体には有害なガスを発生します。だからそんな有害物質を使わないものづくりが必要となってきた。それがハロゲンフリー。
ある基板メーカーと組んで共同開発をして、国内大手家電メーカーS社さんに納めました。S社さんは、それを使ってあのハンディーカメラを製品化して、ハロゲンフリーの流れを作ったわけです。新聞の一面に広告がデカデカと出ていて。うれしかったですよ。この中に入っているんだぞってね。そしてそのハロゲンフリーができた頃には3機目の塗工機が立ち上がり、拡大路線に乗っていきましたね。
若いときから開発テーマを任せられ、課題解決にチャレンジできる社風
何かを解決するたびにお客さんが増えて、塗工機も増えていく。そういう流れですね。
藤田:ちょうど2000年頃だったかな。FPC材料が売れ始めたのは、FPC材料を必要とする製品が増えていったからです。その時代は軽薄・短小っていう、とにかく小さく薄くするという動きが世の中であって、需要自体が広がったということが非常に大きいですね。
当時の開発はすごかった。確か6人ほどいたのですが、みんなそれぞれのテーマを持っていて、私なんか入社して間もないのに、1つのテーマを任せてもらいました。1つのテーマをチームで開発じゃなくて、1人でやるわけです。もう人が足りなくてね。私のような若い技術者が、お客さんのところに行って、こんなものができましたって提案するわけです。すごい会社だなぁと思いました。でも、そうしないと需要に追いつきませんでした。
若いのにいきなり仕事を任せてもらって、チャレンジさせてもらえる社風があったのですね。
北:ありましたね。お客さんの方も売り上げが右肩上がりに伸びている時期でしたから、すごく急いでいたわけです。そこに答えを出して持っていく、すぐ採用になる、そういうサイクルがすごくうまく回っていたなと思います。
(後編に続く)