
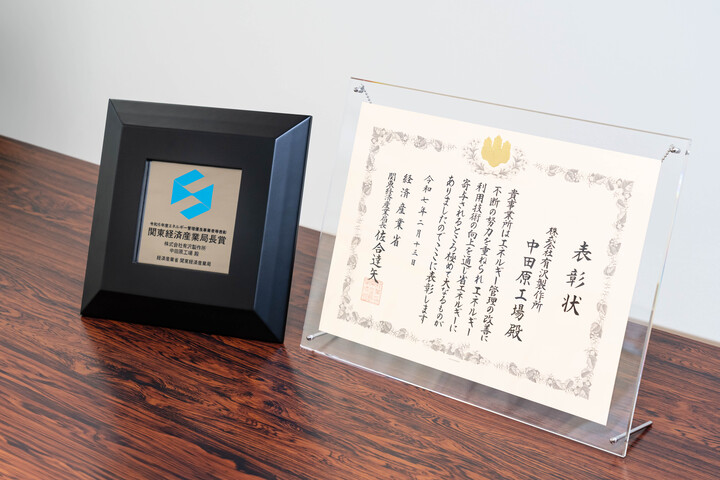
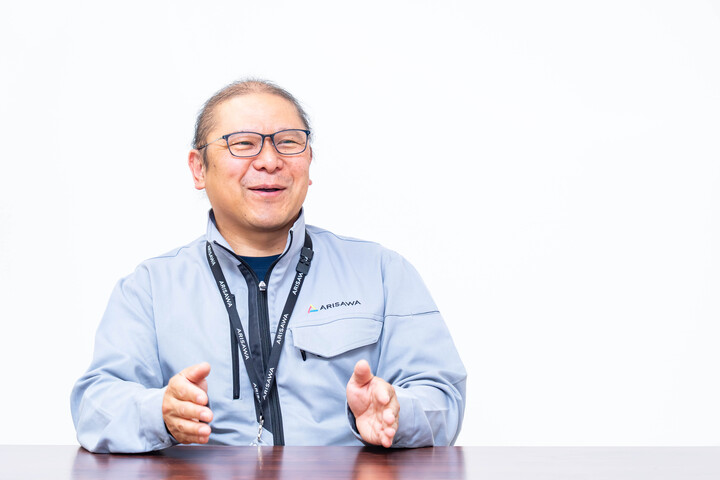
1人や1グループだけではできない、生産技術部門全員で取り組む省エネ活動
その原単位を削減する中で、今回当社はどのような努力をして評価されたのでしょうか。田邉:当社はエネルギーとして主に電気と都市ガスを使用していますので、これらの使用量をいかに削減できるかに知恵を絞ります。生産技術部には電気を専門とするグループ、設計グループ、設備のプログラムを作る計装グループなど、たくさんのグループがあり、メンバーがいます。全員がそれぞれの強みを発揮しながら協力して知恵を絞るのです。全員で協力しながら、大きな設備改修から小さな改善まで本当にさまざまな省エネ活動をしています。例えば生産設備に付いている乾燥ゾーンやチラー(冷却装置)の改造、高効率な空調設備やボイラー設備の導入、電灯のLED化、工場の排熱回収にいたるまで、思いついたことは何でもトライしました。もちろん効果の高かったものもありますし、思ったほど効果の出なかったものもありますが、全体としてはおおむね狙い通りの結果が得られたと思います。当局からは数値的な結果だけでなく、こうしたさまざまな施策にトライした姿勢なども評価していただいたのではないかと思っています。
大変な努力をされたのですね。ちなみに、排熱回収というのは具体的にはどのような改善なのでしょう。
田邉:当社では塗工機という生産設備が多く使用されているのですが、その塗工機は生産過程で高い熱を出します。これまでその熱は排熱として工場の外へ排気していたのです。一方で、製品を乾燥する工程では外から給気して都市ガスを使って空気を温めている。冬場の外気は10℃以下、寒い日であれば0℃以下の日もあります。すでに工程の中で100℃以上に温められている空気を捨てて、わざわざ0℃の空気を取り入れてエネルギーを使って温めていたのです。そこで温められた排熱を再利用するようにしました。この排熱回収という手法は、じつは省エネの世界では定番中の定番なのですが、これまでは安全性や品質保証の観点から手を付けてきませんでした。しかし、高性能なフィルターを介して吸気するなど、これらの改善に目途がついたことから、ようやく排熱回収という全体最適を考えた改善ができるようになりました。
今回表彰されたのは5年間の省エネ実績だと聞きました。5年間でどれほどの省エネ効果があったのですか。
芥川:年の平均値で公表しているのですが、電気が466,671Wh/年、都市ガスが1,011,118㎥/年です。先ほど出てきた原油換算量でいうと1,290kl/年の効果が出ました。ちなみに、5年前と比較するとおよそ10%の削減量となりました。5年で10%ということは、年平均が2%の削減率ということになります。
国の定めた目標値が1%/年ですから、2倍の削減実績です。相当に苦労があったのではないですか。
芥川:一番苦労した点は、生産を止めずに設備を更新しなければならなかったことですね。生産を止めて工事するのが一番楽なのですが、それでは生産計画に遅れが出てしまいます。そういった不具合を出さずに設備更新するというのが、私たち生産技術部門の腕の見せどころだと思っています。例えば空調設備を更新するときなどは、クリーンルームの中で設備だけをビニールカーテンで囲ってその中で作業をしたり、どうしても機械を止めなければならない時は、定期点検や制御更新のある休日に作業したりといったように。しかし、工事業者にはクリーンルームでの作業に慣れてない会社もあって、そういった業者には細かい作業指導をしながらやらなければならないなど、見えないところでたくさんの苦労がありました。生産技術部のメンバーの協力がなければできなかったと思っています。
できることはまだある。まずはデータの可視化を徹底する
なるほど、カネをかければいいということでもないのですね。投資対効果も考えないといけない。
芥川:その通りです。常に省エネへの投資金額とその効果、また工事による生産への影響など総合的に判断しなければなりません。省エネのことを考えるだけでいいのなら、何も作らない、工場を動かさないのが一番の省エネですが、それを言ったらおしまいです。何も解決しない(笑)。
今後は具体的にどのような省エネ対策を考えていますか。当社は2030年度にカーボンニュートラルを達成すると宣言しています。省エネ対策がそこの一丁目一番地です。
田邉:化石燃料を再生可能エネルギーに転換することをもっと考えなければなりません。太陽エネルギーの活用はさらに進めていきます。一部、工場の屋根にソーラーパネルを乗せたりしていますが、まだまだ設置の余地は多い。これを増やしていく計画です。もちろんソーラーだけでなく、水素やバイオマス燃料をエネルギーとしてどの程度活用できるのかも検討を進めています。また、エネルギー消費量そのものを削減することも必要です。建屋内の電灯はまだ蛍光灯のところがあります。これをすべてLEDに変更していきます。ただ問題は、どこの蛍光灯をLEDに変更するといった局所的な話ではなくて、工場全体で、または会社全体でどれほどLED化が進んでいるのかなど、その進捗度が把握できていないことにあります。会社全体を見渡すと、思ったより進んでいるところと、そうでないところがあって、それらをきちんと把握する、つまり「見える化」しなければいけないのです。もちろんLEDだけでなくて、エネルギー全体でそれを進めなければなりません。電気も都市ガスも含めてエネルギーデータ全体の可視化がこれから重要になっていきます。
エネルギーデータがまだ可視化できていないということですか。それは意外でした。
芥川:当社は創立100年を超える製造会社です。古い工場や生産設備がたくさんあります。そこで使われているエネルギーを細かく設備ごとに計測できているかといえば、できているところもあれば、できていないところもある。古い工場ですと、メーターが結構おおざっぱに設置してあったりして、詳細を計測できていません。今後はこれらをきちんと可視化して、従業員全員に分かりやすく見せていく方法を考えていかなければならないと思っています。空調とか、排熱利用とか、設備を変えることでドカンと省エネを進めるといったものだけではダメで、これからは従業員一人ひとりの意識改革も重要になってくる。そういった意識改革につながる仕組みを作っていくのも大事な仕事になってくると考えています。データの可視化もその一つです。
総力戦ですね。
田邉:まさに。省エネは設備だけでなく、それを使う人間も含めてすべての要素を総動員して取り組むべき課題です。そのための意識改革も進めていきます。意識改革といえば、当社では「新製品」という言葉の定義を変えることによって、省エネがモチベーション向上につながる工夫もしています。
どのような工夫ですか。
田邉:一般的には世の中にない製品や自社でこれまで製造していなかった製品を新製品と呼びますよね。しかし当社では、従来の製法を工夫して消費エネルギーを削減できた製品も新製品としてカウントするようにしました。これは私たちのような研究開発部門ではない生産技術部門でも新製品開発に携わることができるということです。やはり製造業に身を置く者としては、新製品の開発に携わってみたいという思いは強い。だからこうした定義の見直しはモチベーション向上につながっています。当社では従来から新製品開発賞という表彰の制度があって、それは研究開発部門が主な対象でした。それが今後は環境価値を付加することでも新製品開発賞にエントリーできるようになる。こうした取り組みを増やすことで、どんどん省エネに対する全社の意識改革につながっていってほしいと思っています。
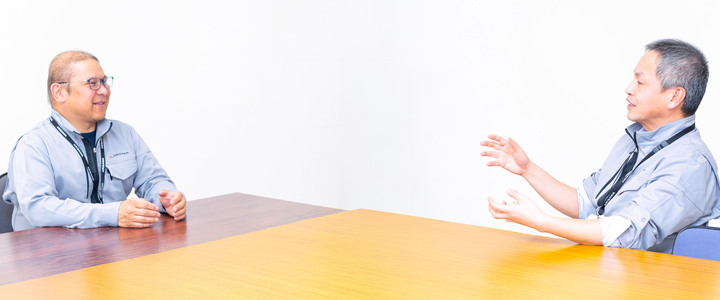